为了给您提供更全面的南阳【本地】铝合金型材管线管层层质检产品信息,我们上传了最新的产品视频。请花几分钟时间观看,您会发现更多惊喜。
以下是:南阳【本地】铝合金型材管线管层层质检的图文介绍
恒永兴金属材料销售
有限公司以雄厚的技术力量,精良的 南阳H型钢、先进设备,完善的制造工艺,严格的 南阳H型钢、质量管理体系,为用户提供优质可靠的产品,可靠的 南阳H型钢、产品质量,良好的售后服务,深受用户的好评, 南阳H型钢、产品覆盖广东、湖北、湖南、广西、大连、东北三省、四川、山东、等二十多个省、市自治区。



1、合金铝板等铝合金型材的技术特点与优势:(1)合金铝板等铝合金型材技术特点:无烟镜面抛光具有无黄烟、无流痕、低成本、低消耗、低设备投入、高亮度、高稳定性、高功效、高成品率等特点,突破了传统抛光技术的瓶颈和缺陷,成功实现了11米长材化学抛光以及自动线化学抛光的规模化生产。无烟镜面抛光技术是普通三酸和电解抛光的升级换代技术,是合金铝板等铝合金型材化学抛光技术的发展方向。(2)合金铝板等铝合金型材技术优势如下:1)无黄烟:无烟镜面抛光从根本解决了三酸抛光产生大量黄烟的难题。可节约大量的环保处理成本。为化学抛光的广泛运用扫清了主要障碍。2)无流痕:无烟抛光技术彻底解决了抛光流痕的难题、并实现了11米长抛光材的全自动线规模生产,使抛光像碱蚀一样易于操作。3)高亮度:无烟抛光由于采用新的抛光成分,比三酸抛光、电解抛光的亮度提高20%~30%,是目前亮度*高的抛光技术。4)低消耗-无烟镜面抛光药剂的消耗可比电解抛光的消耗(500-700kg/t材)降低60%-70%。5)高成品率:无烟镜面抛光过程中几乎不产生缺陷,产品成品率极高。6)生产效率高:无烟抛光挂料而积大,每次可抛光多排;抛光无废品,生产效率至少是三酸抛光的2倍以上,是电解抛光的6-9倍。7)槽液稳定:无烟镜面抛光槽几乎不调槽,可长期稳定工作。为化学抛光铝材的大规模工业化、自动化生产铺平了道路。8)亮度稳定:不同批次生产抛光材,由于不调槽,所生产的抛光材亮度稳定。2、工艺漓程与操作要点分析:(1)槽位设置说明:1)无烟镜面抛光槽前是完全封闭的抽风墙,杜绝外界自然风降低抽风效率,利于阴雨天、浓雾天的全天候生产。2)无烟镜面抛光槽的宽度为1.6m以上,加强槽液吸收烟雾的缓冲能力,利于大规模批量生产。(2)槽液功能说明:1)除蜡除垢槽:本槽中盛一种新型弱碱性除蜡除垢剂,能去机械抛光蜡及残存的重油垢,不腐蚀铝合金。操作简单。2)无烟镜面抛光槽:本槽含有多种组分,富古强氧化剂,能对铝合金进行镜面抛光。与其他抛光技术相比,本槽具有如下特点:①绝无黄烟,亮度稳定:本槽添加有足够量的烟雾抑制剂,黄烟的分解被彻底抑制;由于强氧化剂分解较慢,浓度比三酸槽稳定,因此不同批次铝合金的亮度差别比三酸抛光要小得多。②亮度增加:化学抛光的亮度,陈了与磷酸浓度、硝酸浓度,温度有关外,还与抛光液的含水量有关。含水量越高,亮度越低;三酸抛光液中磷酸含量高达80%(磷酸的含水量为15%),相应抛光液水含量小低于12%;如此高的水含量必然降低抛光材的亮度。无烟镜面抛光液在制作过程中,经过长时间的高温浓缩,水含量水足5%,因此镜面抛光材的亮度明显提高。③可长时间滴流:考虑到化学抛光反应过于剧烈,铝合金离开槽液后,滴流时间不能超过20s,大量抛光液被带进水洗槽,造成抛光材成本过于昂贵。无烟镜面抛光液中添加有足够量的缓蚀剂,保护铝合金离开槽液后,可在空中按任意时间滴流而不花材,也没流痕。由此可节约抛光液70%以上。④自动除灰:铝合金不纯或抛光液老化时,铝材经三酸抛光后,表面往往有一层黑灰,一般方法很难除去,严重影响抛光材质量。无烟镜面抛光槽中,添加有除灰成分,可自动清除抛光灰。⑤成品率高:由于镜面抛光槽解决了色差、流痕、花材、抛光灰等问题,使得成品率大幅提高。从而降低了成本,提高了生产效率。3)保光氧化槽。设置本槽有两大目的:①预制化学氧化膜:保光氧化槽,能生成一定厚度的氧化膜,又能完全保留原有亮度;钢合金从镜面抛光到阳极氧化之前,可以过保光氧化槽,预制一定厚度的化学氧化膜,避免氧化之前在水洗槽中产生点蚀或花材,提高成品率,同时在进行阳极氧化时,减少氧化失光。②精除灰:抛光灰的来源有两种,一是铝合金中有夹杂,二是抛光液老化。抛光灰用一般方法很难清除,能严重影响抛光材的外观质量。尽管无烟镜面抛光槽中已添加有除灰剂,能清除绝大部分抛光灰,但仍可能有少量残留抛光灰。保光氧化槽能彻底清理抛光灰,从而保证抛光材质量。


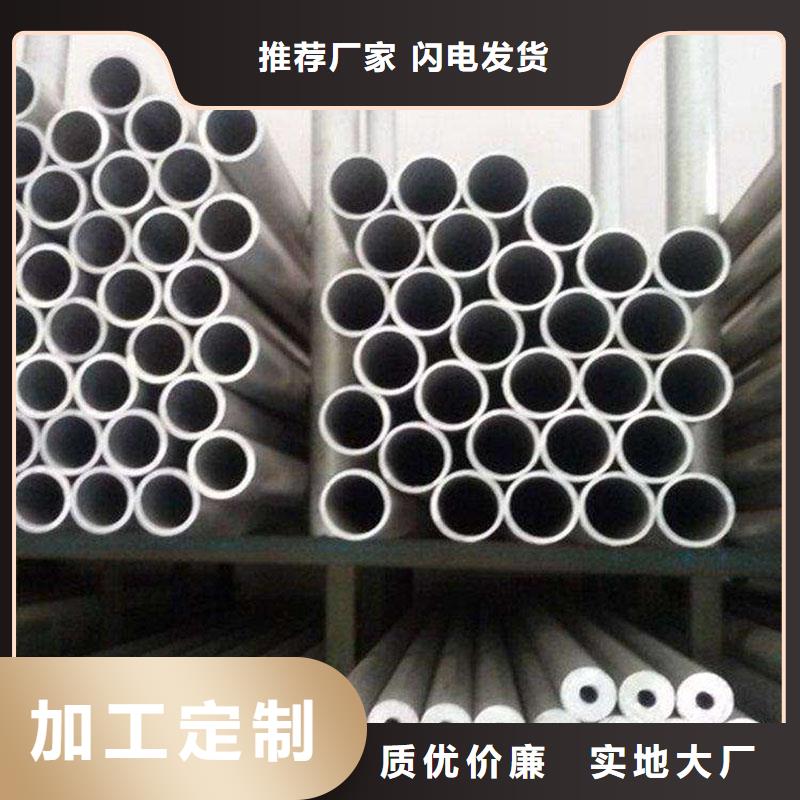
工业铝型材表面经过氧化后,外观非常漂亮,且耐脏,一旦涂上油污非常容易清洗,组装成产品时,根据不同的承重采用不同规格的型材,并采用配套铝型材配件,不需要焊接,较环保,而且安装、拆卸,轻巧便于携带、搬移极为方便。相对于其他金属材质而言,铝型材的可塑性强,生产性好,对于生产制作有很好的优势;铝型材具有很好的延展性能,可以与很多金属元素制作轻型合金,材质优质;铝型材具有模组化和多功能化,可快速架构出理想机械设备外衣。表面处理性能良好,外观色泽艳丽,无需油漆,弹性系数小,碰撞摩擦不起火花,在汽车工艺中表现*佳,没有金属污染,没有毒性。工业铝型材用途广泛,例如:1、建筑用铝型材:建筑铝型材主要包括门窗铝型材和幕墙铝型材;2、散热器铝型材:主要应用于各类电力电子设备散热、LED照明灯具散热、及电脑数码产品的散热等。3、工业铝型材:一般工业铝型材是指主要用于工业生产制造用的,如自动化机械设备、封罩的骨架以及各公司根据自己的机械设备要求定制开模,比如流水线输送带、提升机、点胶机、检测设备、货架等等,电子机械行业和无尘室等。4、汽车零部件铝型材:主要用于汽车零部件、连接件等。5、家具铝型材:主要用于家具装饰框、桌椅支撑件等6、太阳能光伏型材:包括太阳能铝型材边框、太阳能光伏支架、太阳能光伏瓦扣件等。7、轨道车辆结构铝合金型材:主要用于轨道车辆车体制造。8、装裱铝型材:制作成铝合金画框,装裱各种展览、装饰画。9、医用设备铝型材:主要应用于:担架车框架、医疗器械、医疗床等。
铝合金压铸件可以被制造为压铸汽车配件、压铸汽车发动机管件、压铸空调配件、压铸汽油机气缸缸盖、压铸气门摇臂、压铸气门支座、铸电力配件、压铸电机端盖、压铸壳体、压铸泵壳体、压铸建筑配件、压铸装饰配件、压铸护栏配件、压铸轮等等零件。....铝合金压铸件可以被制造为压铸汽车配件、压铸汽车发动机管件、压铸空调配件、压铸汽油机气缸缸盖、压铸气门摇臂、压铸气门支座、铸电力配件、压铸电机端盖、压铸壳体、压铸泵壳体、压铸建筑配件、压铸装饰配件、压铸护栏配件、压铸轮等等零件。随着国内制造装备业发展水平的不断提高,压铸机的装备水平也显著提高,可以制造的零件种类也在不断得到扩大,压铸出来的零件的精度、零件的复杂程度也得到了较大的提升。铝合金压铸件擦伤问题是难以避免的。特征是顺着脱模方向,由于金属粘附,模具制造斜度太小而造成铸件表面的拉伤痕迹,严重时成为拉伤面。
产生原因:1、合金粘附模具。2、铝合金中含铁量低于0.6%。3、铸件顶出偏斜,或型芯轴线偏斜。4、型芯、型壁有压伤痕。5、型壁表面粗糙、6、型芯、型壁的铸造斜度太小或出现倒斜度。7、涂料常喷涂不到。排除措施:1、修正模具,保证制造斜度。2、打光压痕。3、合理设计浇注系统,避免金属流对冲型芯、型壁,适当降低填充速度。4、修正模具结构。5、打光表面。6、涂料用量薄而均匀,不能漏喷涂料。7、适当增加含铁量至0.6~0.8%。铝合金压铸件可以被制造为压铸汽车配件、压铸汽车发动机管件、压铸空调配件、压铸汽油机气缸缸盖、压铸气门摇臂、压铸气门支
智能化焊接的应用前提工业铝型材材料制作的车体具有重量轻、耐腐蚀、外观平整度好及材料可再生利用等优点,因而受到世界各城市交通公司和铁道运输部门的青睐。工业铝型材车体在高速铁路车辆制造上具有不可替代的功能,因此工业铝型材车体的发展速度特别快。目前,全铝结构工业铝型材车辆已经广泛应用于我国铁路车辆动车组的制造和城市轨道交通车辆的制造,尤其高速动车组的钢结构全部是工业铝型材车体,应用*为广泛。在工业铝型材车体制造过程中,由于结构大量采用型材拼接,接头长且规则,便于自动化作业的实现,因此在该行业大量使用各种智能化焊接技术。智能化焊接在动车组工业铝型材车体上的应用实例:2001年,我公司建成了国内 条工业铝型材车体自动化焊接生产线,并利用国产材料,先后开发制造了210km/h工业铝型材车体电动车组、270km/h工业铝型材高速试验列车等动车组工业铝型材车体。2002年,实现了可批量生产工业铝型材车体生产的硬件条件。2004年,我公司从法国阿尔斯通公司引进了200km/h工业铝型材车体动车组CRH5。在成功引进200km/h动车组的前提下,又从德国西门子公司引进了300km/h工业铝型材车体动车组CRH3。自动焊在工业铝型材车体焊接中占有举足轻重的地位,它以焊接质量稳定,生产效率高等优点,得到焊接企业的广泛认可。现在,随着公司的发展与壮大,对于智能化焊接领域的需求大幅度提高。我公司高速动车组工业铝型材车体焊接生产,自动焊焊接量约占整车焊接总量的75%。主要采用的智能化焊接技术是自动MIG焊技术和搅拌摩擦焊技术,其中自动MIG焊应用*为广泛,约占自动焊焊接总量的95%,而搅拌摩擦焊还仅处于小面积应用和探索阶段,相在不久的未来,搅拌摩擦焊技术也会得到长足的发展。(1)高速动车组工业铝型材车体结构特点:高速动车组工业铝型材车体,主要分为中间车工业铝型材车体和头车工业铝型材车体。中间车工业铝型材车体主要由底架、侧墙、车顶、端墙等四个部位组成,头车工业铝型材车体主要由底架、侧墙、车顶、端墙及车头等五个部位组成。图1为CRH380型动车组中间车工业铝型材车体,图2为CRH380型动车组头车工业铝型材车体。CRH380型动车组工业铝型材车体,底架组成主要由地板、底架边梁、KK端/FE端、裙板以及各种小件组合而成。车顶主要由圆顶、平顶、车顶边梁、空调框、端顶组成,通过台组成以及各种小件组合而成。侧墙组成主要由侧墙板、门立柱、应接板以及各种小件组合而成。端墙主要由端墙板、端角柱、车顶连接梁、车顶侧弯梁以及各种小件组合而成。车头组成主要由左右侧墙、前墙、前窗框、环形框以及各种小件组合而成。(2)自动MIG焊技术在高速动车组工业铝型材车体制造上的应用:高速动车组工业铝型材车体焊接通常分为车体大部件自动焊、小部件自动焊和总组成自动焊。大部件自动焊一般指车顶板、平顶板、地板、车顶及侧墙自动焊;小部件自动焊一般指端墙、车头、隔墙、裙板及车钩座自动焊;总组成自动焊一般指侧墙和车顶、侧墙和底架连接缝自动焊。工业铝型材车体制造中投入大型关键焊接设备,是制造工业铝型材车体的必备条件。在高速动车组工业铝型材车体的制造过程中,为了提高整机产品的焊接质量,提升焊接生产效率,降低劳动强度,公司曾先后投入了龙门式IGM机械手、悬臂式ESAB专机、SMC专机、FOOKE专机、OTC专机及小型IGM机械手、CLOOS机械手、OTC机械手等自动焊设备,以此实现自动MIG焊接技术的应用。大部件自动焊主要采用龙门式IGM机械手和悬臂式ESAB专机等设备,焊缝跟踪方式为激光跟踪。送丝机构形式分为单丝焊接和双丝焊接,其中,单丝焊接只是用在初期的设备系统上。总组成自动焊主要采用SMC专机和FOOKE专机等设备,焊缝跟踪方式为机械跟踪,送丝机构形式为单丝焊接。小部件自动焊主要采用小型IGM机械手等设备,焊缝跟踪方式为激光跟踪。图3是大型的龙门式IGM机械手,图4是FOOKE专机。在高速动车组工业铝型材生产初期,CRH5型动车组侧墙中间两块板、车顶中间三块板、车顶合成和CRH380型动车组圆顶板、平顶板等部件的生产采用双枪单丝的IGM机械手进行自动焊接;CRH5型动车组侧墙合成部件的生产采用双枪单丝悬臂式的ESAB专机进行自动焊接;底架地板的生产采用双枪双丝的IGM机械手进行自动焊接;端墙板、车头等小部件生产采用CLOOS、小型IGM机械手进行自动焊接。然而,随着动车组产能的扩大和工艺布局的调整,单丝的IGM机械手由于生产效率较低,已被弃用。截止目前,高速动车组所有工业铝型材车体大部件生产采用的都是双枪双丝的IGM机械手进行焊接;小部件生产采用的都是小型IGM机械手进行焊接;总组成自动焊接主要采用SMC专机和FOOKE专机两种设备,其中,CRH5型动车组总组成焊接采用SMC专机,CRH380型动车组总组成焊接采用FOOKE专机。图5是动车组侧墙自动焊接。图6是动车组端墙墙板自动焊接。自动MIG焊技术在高速动车组工业铝型材车体制造上的广泛应用,使得公司的焊接技术水平得以大幅度提高,生产线的制造能力也大大提升,从而保证了高速动车组工业铝型材车体的产品质量,为高铁生产制造领域做出了突出贡献。(3)搅拌摩擦焊技术在高速动车组工业铝型材车体制造上的应用:搅拌摩擦焊是一种固相连接方法,焊接接头具有优良的力学性能和小的焊接变形,焊接过程中不需要添加保护气和焊丝,没有熔化、烟尘、飞溅及弧光,是一种环保型的新型连接技术。实际情况也的确如此,在FSW技术问世后的短短几年内,在焊接机理、适用材料、焊接设备以及工程化应用方面均取得了很大的进展。高铁车身地板搅拌摩擦焊:我公司从2008年初开始,就针对搅拌摩擦焊技术在工业铝型材车体材料上开展试验研究工作,经过反复的试验摸索获得了一定的试验结果后,于2010年7月开始在高速动车组车钩座等关键部件上进行工艺试制。通过试验团队的不断努力,此技术*终于2013年在高速动车组车钩座上取得了实质性的应用,届时使得产品实物质量显著提高,生产效率飞速提升,劳动强度大幅降低,获得了公司上下的一致好评。鉴于该技术的优越性,2014年在中国标准动车组项目研制过程中,搅拌摩擦焊在车体小部件上进行了大面积的推广应用,并取得了良好的经济价值和社会效益,为高速动车组走出去奠定了丰富的技术基础。图7是小部件FSW设备。图8是FSW焊接车钩座。智能化焊接在动车组工业铝型材车体上的推广建议(1)自动MIG焊接技术继续在高速动车组工业铝型材车体制造上应用:由于自动MIG焊接技术现今比较成熟、稳定,所以优先建议其在平顶附件组焊、端墙合成组焊、KK组焊、FE组焊、车头组焊及底架合成组焊等复杂工序继续推广应用。针对部件结构和制造工艺特点,选择合适的自动焊设备,如平顶附件组焊可以利用现有的IGM机械手进行自动焊接应用研究,端墙组焊、KK组焊、车头组焊等小部件工序可以引进机器人并利用变位机的多方向旋转功能实现自动焊接应用。相在不久的将来,在各专业技术专家的不断努力下,我公司能够成为真正意义上的智能化制造企业。(2)加快搅拌摩擦焊的推广应用步伐:搅拌摩擦焊是将来高速动车组工业铝型材车体焊接的发展方向,值得开展相关方面的研究和应用。目前,搅拌摩擦焊在CRH380和CRH5型动车组两个批量生产的项目上,仅在CRH380型动车组车钩座和车钩梁两个小部件上有所应用,建议应向CRH380型动车组端墙板、平顶板和CRH5型动车组垂直墙、水平墙、前端墙等小部件上加快推广应用的步伐。另外,也应在工业铝型材车体大部件(底架地板、侧墙、车顶)上开展FSW基础性的试验研究,如开展型材结构设计、工装夹具开发、搅拌头设计及焊接工艺试验等工作,为将来的实际生产应用积累丰富的试验数据,并打下坚实的实践基础。

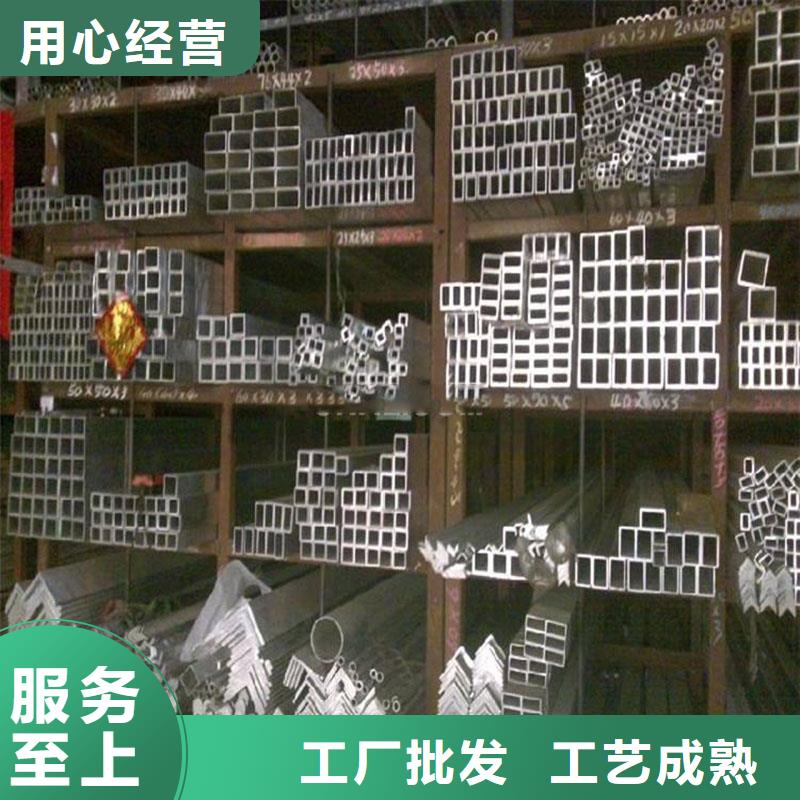
铝及铝合金焊丝的选择主要根据母材的种类,对接头抗裂性能、力学性能及耐蚀性等方面的要求综合考虑。有时当某项成为主要矛盾时,则选择焊丝就着重从解决这个主要矛盾入手,兼顾其它方面要求。一般情况下,焊接铝及铝合金都采用与母材成分相同或相近牌号的焊丝,这样可以获得较好的耐蚀性;但焊接热裂倾向大的热处理强化铝合金时,选择焊丝主要从解决抗裂性入手,这时焊丝的成分与母材的差别就很大。
常见缺陷(焊接问题)及防止措施1、烧穿---产生原因:a、热输入量过大;b、坡口加工不当,焊件装配间隙过大;c、点固焊时焊点间距过大,焊接过程中产生较大的变形量。防止措施:a、适当减小焊接电流、电弧电压,提高焊接速度;b、大钝边尺寸,减小根部间隙;c、适当减小点固焊时焊点间距。2、气孔---产生原因:a、母材或焊丝上有油、锈、污、垢等;b、焊接场地空气流动大,不利于气体保护;c、焊接电弧过长,降低气体保护效果;d、喷嘴与工件距离过大,气体保护效果降低;e、焊接参数选择不当;f、重复起弧处产生气孔;g、保护气体纯度低,气体保护效果差;h、周围环境空气湿度大。防止措施:a、焊前仔细清理焊丝、焊件表面的油、污、锈、垢和氧化膜,采用含脱氧剂较高的焊丝;b、合理选择焊接场所;c、适当减小电弧长度;d、保持喷嘴与焊件之间的合理距离范围;e、尽量选择较粗的焊丝,同时增加工件坡口的钝边厚度,一方面可以允许使用大电流,公众号:焊王,另一方面也使焊缝金属中焊丝比例下降,这对降低气孔率是行之有效的;f、尽量不要在同一部位重复起弧,需要重复起弧时要对起弧处进行打磨或刮除;一道焊缝一旦起弧要尽量焊长些,不要随意断弧,以减少接头量,在接头处需要有一定焊缝重叠区;g、换保护气体;h、检查气流大小;i、预热母材;j、检查是否有漏气现象和气管损坏现象;k、在空气湿度较低时焊接,或采用加热系统。3、电弧不稳---产生原因:电源线连接、污物或者有风。防止措施:a、检查所有导电部分并使表面保持清洁;b、将接头处的脏物清除掉;c、尽量不要在能引起气流紊乱的地方进行焊接。4、焊缝成型差---产生原因:a、焊接规范选择不当;b、焊枪角度不正确;c、焊工操作不熟练;d、导电嘴孔径太大;e、焊丝、焊件及保护气体中含有水分。防止措施:a、反复调试选择合适的焊接规范;b、保持合适的焊枪倾角;c、选择合适的导电嘴孔径;d、焊前仔细清理焊丝、焊件,保证气体的纯度。5、未焊透---产生原因:a、焊接速度过快,电弧过长;b、坡口加工不当,装备间隙过小;c、焊接规范过小;d、焊接电流不稳定。防止措施:a、适当减慢焊接速度,压低电弧;b、适当减小钝边或增加根部间隙;c、增加焊接电流及电弧电压,保证母材足够的热输入能量;d、增加稳压电源装置e、细焊丝有助于提高熔深,粗焊丝提高熔敷量,应酌情选择。6、未熔合---产生原因:a、焊接部位氧化膜或锈迹未清除干净;b、热输入不足。防止措施:a、焊前清理待焊处表面b、提高焊接电流、电弧电压,减小焊接速度;c、对于厚板采用U型接头,而一般不采用V型接头。7、裂纹---产生原因:a、结构设计不合理,焊缝过于集中,造成焊接接头拘束应力过大b、熔池过大、过热、合金元素烧损多;c、焊缝末端的弧坑冷却快;d、焊丝成分与母材不匹配;e、焊缝深宽比过大。防止措施:a、正确设计焊接结构,合理布置焊缝,使焊缝尽量避开应力集中区,合理选择焊接顺序;b、减小焊接电流或适当增加焊接速度;c、收弧操作要正确,加入引弧板或采用电流衰减装置填满弧坑;d、正确选用焊丝。8、夹渣---产生原因:a、焊前清理不彻底;b、焊接电流过大,导致导电嘴局部熔化混入熔池而形成夹渣c、焊接速度过快。防止措施:a、加强焊前清理工作,多道焊时,每焊完一道同样要进行焊缝清理;b、在保证熔透的情况下,适当减小焊接电流,大电流焊接时导电嘴不要压太低;c、适当降低焊接速度,采用含脱氧剂较高的焊丝,提高电弧电压。9、咬边---产生原因:a、焊接电流太大,焊接电压太高;b、焊接速度过快,填丝太少;c、焊枪摆动不均匀。防止措施:a、适当的调整焊接电流和电弧电压;b、适当增加送丝速度或降低焊接速度;c、力求焊枪摆动均匀。10、焊缝污染---产生原因:a、不适当的保护气体覆盖;b、焊丝不洁;c、母材不洁。防止措施:a、检查送气软管是否有泄漏情况,是否有抽风,气嘴是否松动,保护气体使用是否正确;b、是否正确的储存焊接材料;c、在使用其它的机械清理前,先将油和油脂类物质清除掉;d、在使用不锈钢刷之前将氧化物清除掉。11、送丝性不良---产生原因:A、导电嘴与焊丝打火;b、焊丝磨损、喷弧;d、送丝软管太长或太紧;e、送丝轮不适当或磨损;f、焊接材料表面毛刺、划伤、灰尘和污物较多。防止措施:a、降低送丝轮张力,使用慢启动系统;b、检查所有焊丝接触表面情况并尽量减少金属与金属的接触面;c、检查导电嘴情况及送丝软管情况,检查送丝轮状况;d、检查导电嘴的直径大小是否匹配;e、使用耐磨材料以避免送丝过程中发生截断情况;f、检查焊丝盘磨损状况;g、选择合适的送丝轮尺寸,形状及合适的表面情况;h、选择表面质量较好的焊接材料。12、起弧不良---产生原因:a、接地不良;b、导电嘴尺寸不对;c、没有保护气体。防止措施:a、检查所有接地情况是否良好,使用慢启动或热起弧方式以方便起弧;b、检查导电嘴内空是否被金属材料堵塞;c、使用气体预清理功能;d、改变焊接参数。

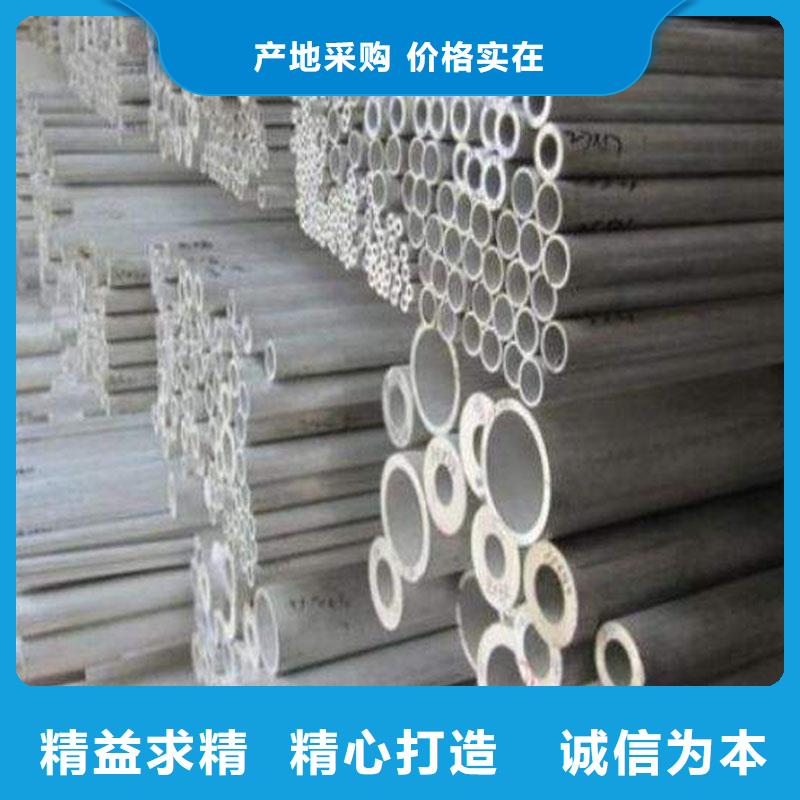
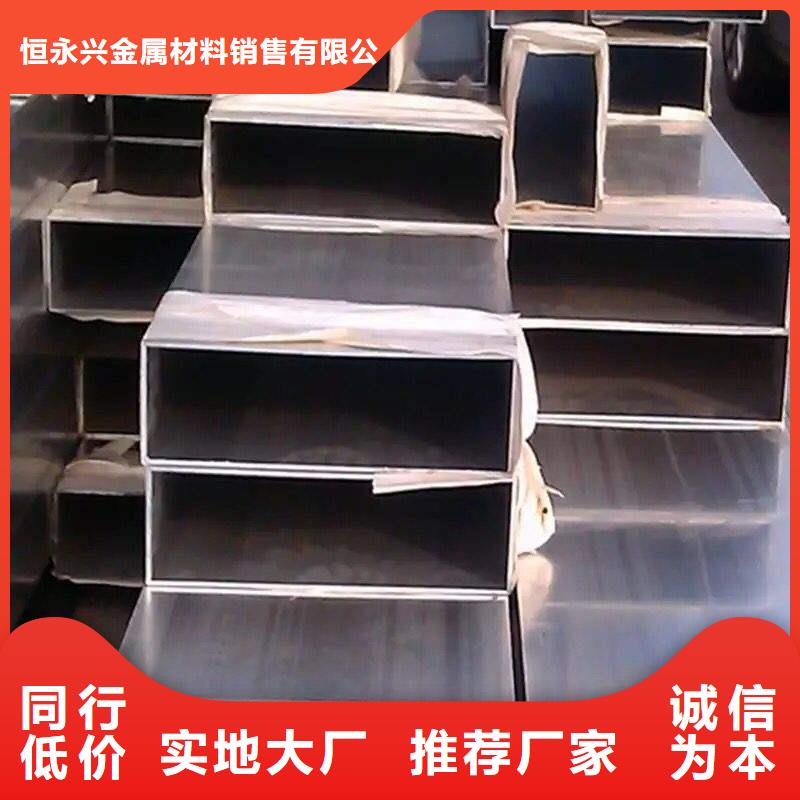